
Multipurpose Exoskeleton Platform
Aug 2017 - May 2018
To develop an exoskeleton platform actuated by Series Elastic Actuators for both medical and industrial purposes with engineers from SuitX. Unlike traditional single-purpose exoskeletons, such modularized platform can adapt to various applications.
Responsible for designing exoskeleton by gathering engineer’s and customer’s specifications.
Developed a multipurpose exoskeleton platform that can be used for both medical and industrial applications based on the last iteration of SuitX's powered exoskeleton.
Launched cross-application frameworks for teaming, communication, timelines, etc.
Led and organized team meetings to produce reporting deliverables ahead of schedule.
Developed system to generate design parameters from gait data.
Optimized hip design to avoid singularity of series-elastic actuator (SEA).
Designed SEA and electronics housing to consider wire routing and heat dissipation.
Designed hip bumpers for patient-specific customization and cross-application cost reduction.
Generated engineering drawings and assembled prototype hip assemblies.
Leveraged user interviews, roadmapping and other human-centered design methods.
Responsible for contacting the supplier and provided requirement documents for manufacturing.
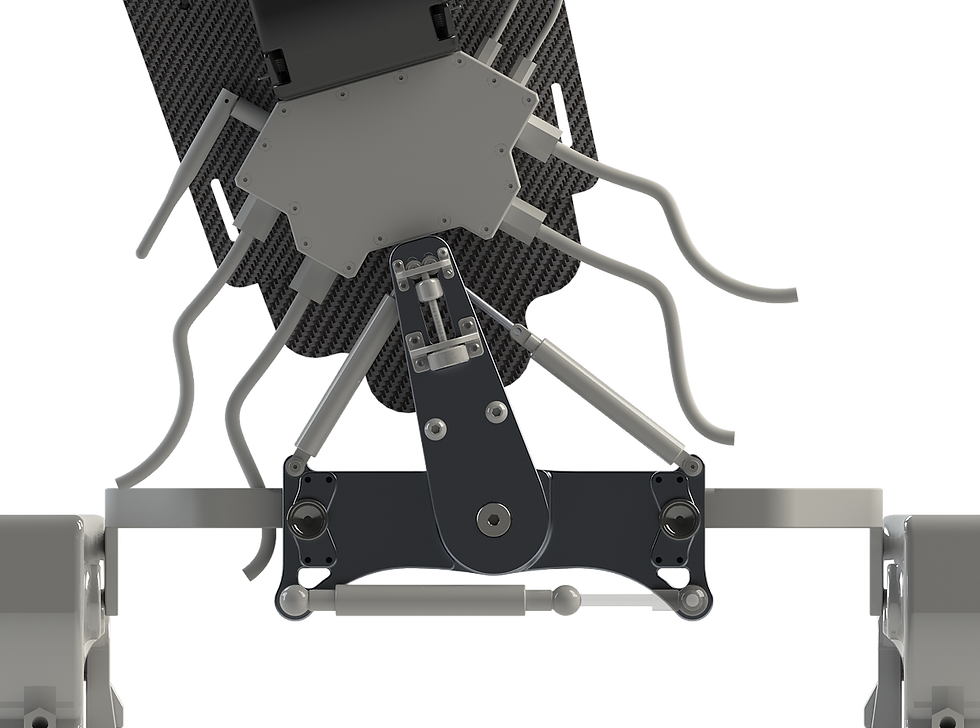
The primary goal of this project is to develop a lower-limb exoskeleton prototype which can be outfitted to either rehabilitate stroke survivors or augment relief workers in post-disaster operations. This shared, modular platform will additionally integrate with exoskeletons from our industry sponsor, SuitX, to reduce costs through volume and manufacturing efficiency. We are also leveraging a low profile, high-efficiency series elastic actuator (SEA) and reducing the overall number of sensors from previous designs, in order to further cut costs.
One application of this system is for the walking rehabilitation of stroke survivors. The success of stroke rehabilitation therapy is heavily dependent on its frequency and timeliness after a stroke. Using devices alongside conventional therapy can increase the time spent exercising, which is currently restricted by insurance coverage and therapists’ availability. However, the cost of contemporary devices has prevented mass adoption. Such devices typically cost between $70K and $120K. Our goal is to design an exoskeleton for production below $15K, making it more viable for clinical use and opening up an entire market of at-home users.
The other primary application is as an assistive device in post-disaster (PD) situations. The success of post-disaster search and rescue operations depends on the availability of sufficient physically capable human labor, equipment for moving heavy objects and debris, and transportation routes accessible immediately after the disaster. The absence of sufficient physically-capable human labor to move debris at disaster sites prolongs the rescue process, which can be the difference between saving and losing lives. Our solution is a class of robot exoskeleton systems to help relief workers traverse rough and unstructured terrain while carrying survivors or supplies. As with stroke exoskeletons, cost of has been a primary barrier to adoption. By designing a system that can be produced for less than $15K, we can commercialize our augmentative technology at a high volume, for relief operations around the world.